Products > Waste Water Treatment (for ETP & STP ) >Electrolytic System >> |
|
Advanced Oxidation Unit:- |
 |
|
|
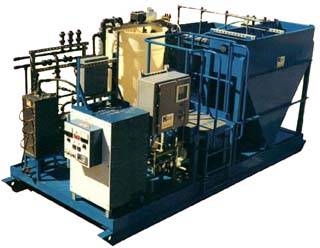 |
|
Introduction:- |
 |
|
|
The advanced oxidation process (AOP) is successfully used to decompose many hazardous chemical compounds to acceptable levels, without producing additional hazardous by-products or sludge which require further handling. Advanced Oxidation Process enhances the efficiency of ozone by producing hydroxyl radical. "AOP" system is more effective & uses less ozone as compared to conventional ozone treatment. We use ozone in presence of a catalyst to treat large flow-rates of wastewater to control Color, Biological oxygen demand, Chemical oxygen demand, Fats, oils & grease etc and the treated water can be recycled. |
|
Working Principle:- |
 |
|
|
The term advanced oxidation processes refers specifically to processes in which oxidation of organic contaminants occurs primarily through reactions with hydroxyl radicals. AOPs usually refer to a specific subset of processes that involve O3, H2O2, and/or UV light. The most widely applied advanced oxidation processes (AOP) have been: |
|
|
- Peroxide/ultraviolet light (H2O2/UV)
- Ozone/ultraviolet light (O3/UV)
- Hydrogen peroxide/ozone (H2O2/O3)
- Hydrogen peroxide/ozone/ultraviolet (H2O2/O3/UV) processes
|
|
Applications:- |
 |
|
|
- Gas effluent treatment
- water reclaim / reuse / recycling
- drinking water supplies
- industrial & municipal wastewater
- process water, ultra-pure water
- electronic & pharmaceutical industries
- medicinal baths, sanatoriums, hospitals
- cooling water systems
- fish hatcheries and farm.
- Pharmaceutical waste
|
|
Advantages:- |
 |
|
|
- Advanced oxidation process needs less ozone and provides better results as compared to conventional ozone treatment.
- Reduction in ozone requirement & residence time makes these systems economical to treat large flow-rates.
- Up to 95% reduction of waste load (COD, BOD, TOC etc).
- Total Color removal.
- Efficient removal of organic matter such as dyes, surfactants, proteins, oils & grease etc.
- Treatment and recycling of waste waters in textile industry, petroleum industry, food industry etc.
- No offensive odors.
- Automatic system.
- Rapid reaction rates
- Small foot print
- Potential to reduce toxicity and possibly complete mineralization of organics treated
- Does not concentrate waste for further treatment with methods such as membranes
- Does not produce materials that require further treatment such as "spent carbon" from activated carbon absorption
- Does not create sludge as with physical chemical process or biological processes (wasted biological sludge)
- Non selective pathway allows for the treatment of multiple organics at once.
|
|
|